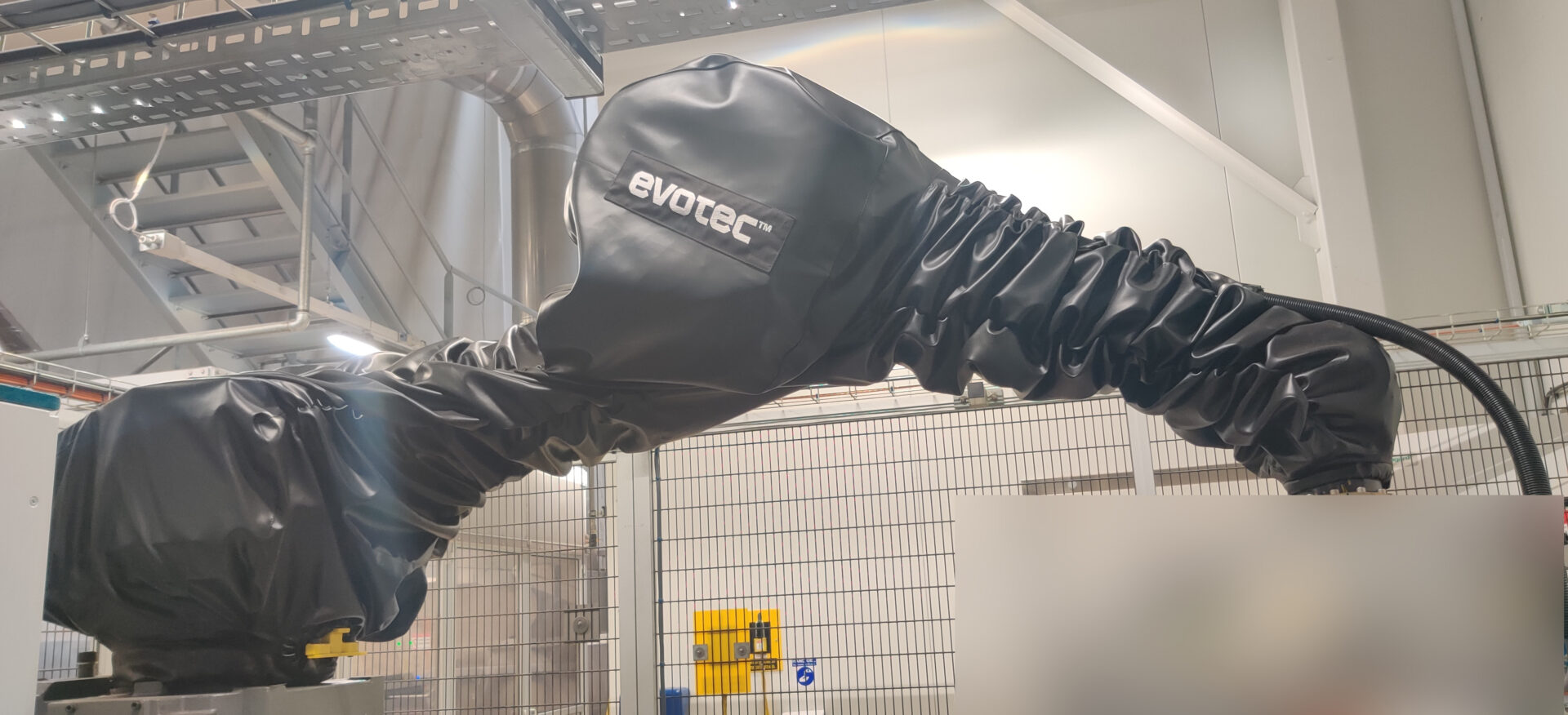
5 reasons why you should implement protective covers ![]()
Manufacturers rely on industrial robots due to the challenges of finding skilled workers and rising labour costs. While robots offer […]

Find the solution
We will provide you with a tailor-made solution for your needs. Leave your contact details and we will get back to you within 24 hours.
Welding processes usually generate harmful factors such as welding sparks and spatter, as well as heat radiation and dust. These factors can have a detrimental effect both on the operation of industrial machinery, such as robots, and on the safety and comfort of human workers. Fortunately, the harmful effects can be significantly reduced through the use of covers such as welding curtains and welding robot covers. The welding curtain is mainly intended to separate the welding station from the rest of the production facility, blocking the spread of dirt, weld spatter and light flashes, while protective covers shield the machines exposed to such factors.
Protective covers for welding robots help keep robots working in the welding process in good technical condition. The non-flammable material of the cover effectively protects the machine from the harmful effects of welding sparks and spatter, while the reflective coating reflects part of the heat radiation, reducing the risk of overheating. Additional cover parts such as cable covers and actuator covers increase the level of safety in production by protecting the elements of the equipment most susceptible to damage.
EVOTEC welding covers and shields are simple but effective solutions to help increase the safety level of both machines working in production and human workers. Welding curtains reduce the risk of fire and accidents by blocking the spread of sparks. A cover for a robot working in the welding process helps shield the machine from burns, surface damage and overheating. Both solutions contribute to the cleanliness of the production facility. The use of EVOTEC protective covers makes it possible to significantly improve working conditions in production, both for machines and people.
Let’s talk about what harmful factors your robot is exposed to.
Book a conversation now.